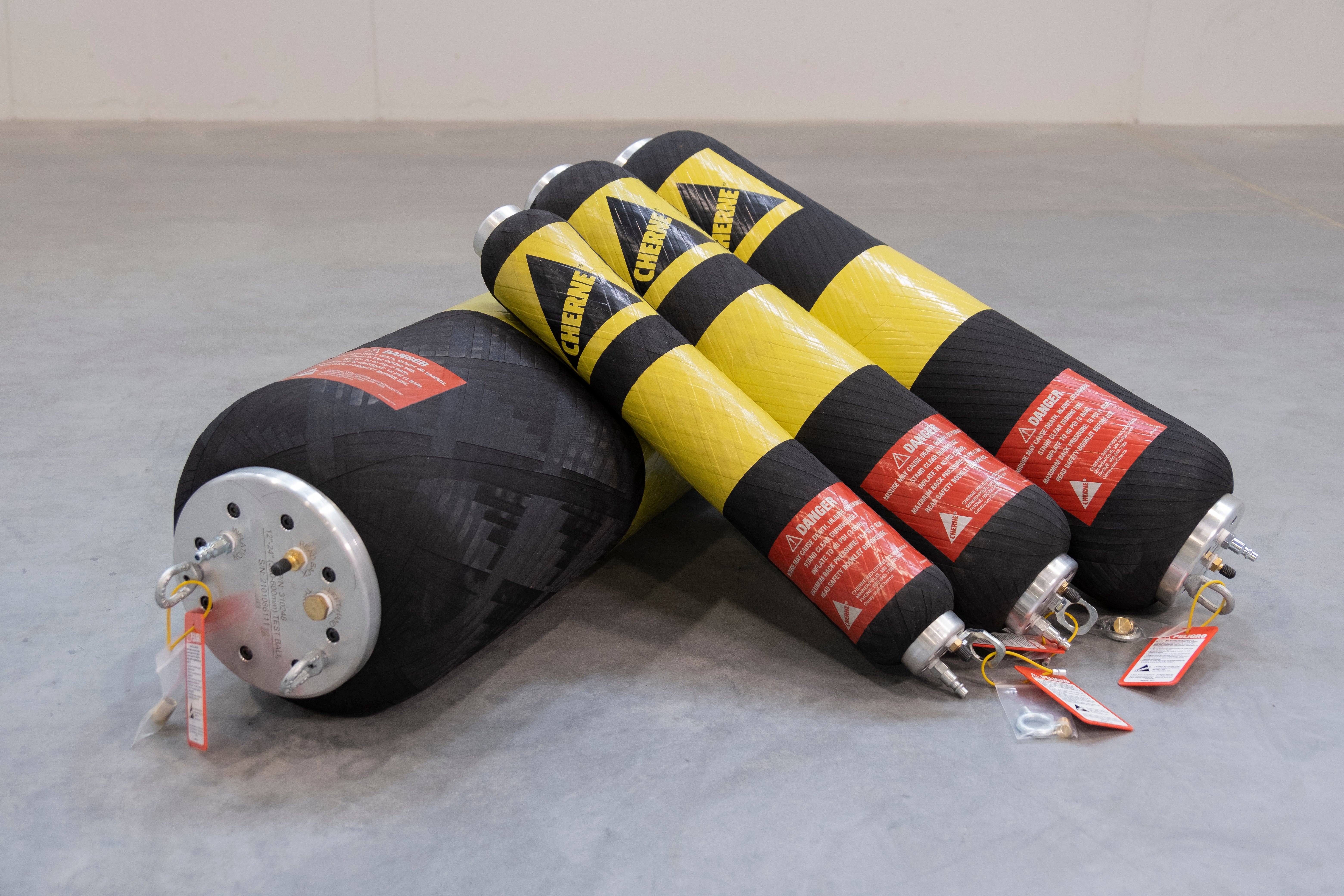
At Cherne Industries, safety is a top priority. We know that on the job, accidents and deaths become even more tragic when you realize they were preventable. Such is the case with the misuse of Cherne’s pneumatic pipe plugs. When using pipe plugs, understanding equipment and job conditions are vital to contractor safety.
Cherne sets the standard for high-quality, reliable pipe plugs. Although these products are built with safety in mind, they are only as safe as the person using them. To practice safe plug usage at all times, contractors must take the time to learn the proper procedures.
Below, we share four vital safety tips and best practices when using Cherne’s pneumatic pipe plugs for municipal or commercial pipeline testing, maintenance and repair. This blog is not a replacement for the product instruction manual that comes with all Cherne products and must be read fully before using Cherne pipe plugs.
1. Never enter the danger zone
When a plug is in use, a danger zone exists that expands outwardly in a cone shape from the manhole opening. The most important safety measure is never to enter the danger zone in such a situation.
Remember that the total force exerted on a pipeline plug is directly proportional to both the pressure and the pipeline area. The amount of force behind a plug can be overwhelming.
To better understand the hidden dangers you may face when entering the danger zone, let’s break down what happens when a plug is used to hold back pressure.
The formula for calculating pipeline forces and pressures is…
Force = Pipeline Area x Pressure
Consider the following examples: an 8-inch plug used in a 4 psi (pounds per square inch) test is subjected to over 250 pounds of force. The same 4 psi test in a 48-inch diameter pipe is restraining over 7,200 pounds of force. Standing in front of a plug during this type of air test would be like standing in front of a loaded cannon with a lit fuse. A plug deflated before the back pressure is released can cause serious injury and even death.
2. Preparation before using pipe plugs
Before beginning any job, be sure to follow the guidelines below to prepare for the usage of pneumatic pipe plugs.
Select the proper plug and related equipment. Every pipe plug has performance specifications listed on the plug and in the product literature.
Determine the back pressure: The maximum back pressure the plug must withstand is the pressure (air or liquid) in front or back of the plug that it must restrain. Never exceed the plug’s back pressure rating. As explained in the previous section, the total force exerted on a pipeline plug is directly proportional to both the pressure and the pipeline area.
Select the correct plug size: Pipe plugs have a minimum and maximum sealing size range. Always verify that the pipe inside diameter (ID) is within the plug’s sealing (usage) range. It’s important to check the ID of the pipe to be plugged and match it to the usage range of the pneumatic plug to make sure it will work in the intended pipe
Correct pipe design: Plug performance could vary, depending on pipe types. For example, in corrugated pipe, plug back pressure rating drops by 50%.
Use calibrated gauges: Failure to use calibrated gauges could result in plug over-inflation or under-inflation of the plug, leading to failure. We recommend monitoring inflation and back pressure with calibrated pressure gauges only. In addition, never deflate a plug while back pressure is still in the line. More importantly, always deflate a plug remotely, using an extension hose. Once again, never deflate a plug within the danger zone.
Properly clean and inspect the plugs: Plugs must be clean and inspected before and after every use. Do not use a plug if it has or shows any signs of wear or deterioration.
The inspection should include, but not be limited to, looking for cuts, abrasions, punctures, bulges, cracks, corrosion, loose or damaged fittings and components, and leaks.
Be sure to inspect the pipe and clear it of any debris or foreign substances before placing the plug in the pipe. Inflation against a sharp object could cause the plug to rupture. An unclean pipe could reduce the plug’s back pressure-holding capability and damage the plug during placement or inflation.
An engineer must determine if a backup system is required and must design a blocking device. An additional backup system should be considered to prevent injury or property damage in case of plug failure. A properly designed blocking device must be used to restrain any plug movement, because forces behind the plug could be tremendous. Never use eye bolts, inflation hoses, or other attachments on the plug as a means to restrain plug movement under back pressure.
3. Monitor the placement and pressure of the plug during operation
While in operation, it is important to monitor the placement and pressure of the plugs.
Never use chemicals, including hydrocarbons, as they can cause damage to the natural rubber. Be sure to use the correct media when inflating the plugs. Cherne plugs can be inflated with air, water, and inert gasses (nitrogen). Never overinflate or underinflate the plugs.
Always release the back pressure from the pipe before deflating the plug. Plug deflation before releasing back pressure could cause the plug to dislodge at extreme velocity.
4. Maintenance and storage
Cherne’s pneumatic plugs can be cleaned with mild soap and water (other cleaning agents may cause damage). Store the plug in a dry place, below 110 degrees Fahrenheit, and away from sunlight or other sources of ultraviolet light and ozone.
Following these simple steps and taking the time to correctly do the procedure can actually make the difference between life and death. Cherne provides safety tags and safety instruction manuals with each plug that leaves our factory. Ensure that you and everyone on your crew are familiar with the hazards and the preventive measures necessary when working with pipe plugs.