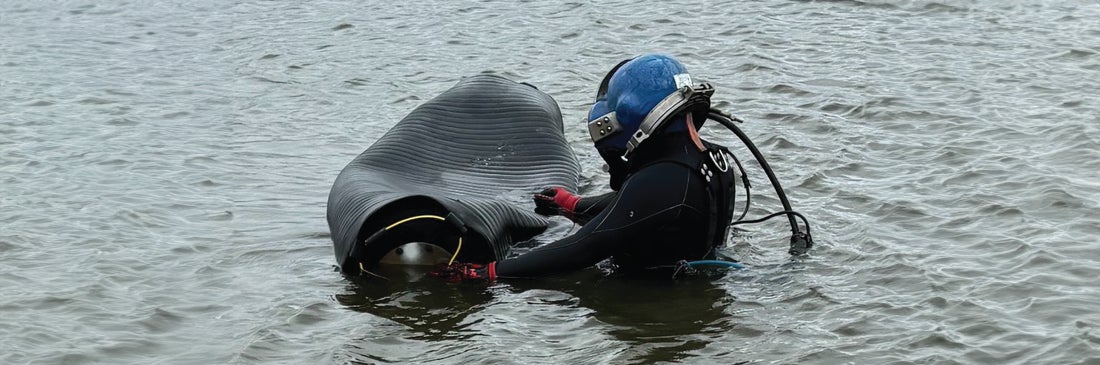
March 4th, 2024
VOLUSIA COUNTY, FLORIDA — As Florida’s population grows, the state’s high water table makes clearing land difficult for real estate developers. To mitigate this issue, the state uses storm systems to capture and redirect excess water. Creating these systems requires construction companies to remove the water initially found during the building process in Florida.
That process demands heavy inspections and strict adherence to the tolerances. These criteria, in turn, require sites to be dried for inspections. Commercial diving companies rely on large pipe plugs to block incoming water flow from municipal pipe systems.
One such company is Central Florida Blackwater Diving, which is owned and operated by Charles Souder. Once a small business, Central Florida Blackwater Diving has grown into a prominent enterprise in its community. In recalling his journey from employee to owner, Souder credits his success to a relentless work ethic and a commitment to relationship building.
“Until I started diving, I was deathly afraid of any body of water—including pools,” he jokes. How he overcame his crippling fear of water to become a highly skilled diver in Florida is shocking, even to himself. At 18, Souders was given an ultimatum by his family: Either attend a university or move out. Instead, Souders decided on a more unconventional route: commercial diving.
“I was afraid until the moment I put the helmet on and tried diving,” he says. “I immediately knew this was my path.”
Using Cherne Blocking Pipe Plugs for Inland Diving Projects
Souders is skilled in both inland shoreline diving and offshore commercial diving. His short stint as an offshore diver in the gulf led him to master the skills and safety components needed to be a great diver. Inland diving, which typically occurs in ponds, lakes, ports, pipe systems, and other shallow waters, has a diving limit of 300 feet before saturation occurs.
As mentioned, Souders relies on large pipe plugs to block incoming water flow via municipal pipe systems. The type of pipe plug Souders uses depends on the size and anticipated amount of water passing through the pipe system. Working with pipe diameters ranging from eight to 96 inches, he typically uses Cherne blocking plugs ranging from 24-48 inches to 24-60 inches.
Waterworks blocking plugs are pneumatic plugs used for blocking the flow during new construction, maintenance, or testing in freshwater, stormwater, or wastewater and sewer systems. For example, Multi-Size Underground Test-Ball Plugs are an economical pneumatic plug option for blocking flow.
The plug is made of natural rubber, allowing for expansion and memory. One plug fits multiple pipe diameters and can seal both round and out-of-round pipe. Each plug has a removable inflation valve that can be replaced if damaged with another inflation valve or with a quick-disconnect fitting.
Expert Preparation for Quality Underwater Pipe Plug Installation
To prepare for a dive, Souders ensures all his equipment works properly. He says there are three main tools needed to install a new plug.
First, he uses a vacuum system to force high-pressure air to suck out the plugs, causing them to sink. Next, he uses an active air fill gauge to ensure proper pressure. “If there is too little pressure, the plug will not hold,” Sauder explains. “Too much will cause the plug to blow.”
Finally, he brings dredging equipment to clean dirt and other obstructions that can cause plug damage or compromise the seal. These steps are his formula to ensure the utmost quality for his clients.
Once he has started his dive, Souders and his team on land work together to inflate the pipe plug while he stays below water to ensure the pipe remains stable, doesn’t collapse, and achieves a proper seal. He then ensures the plug is fully inflated, the fittings are all airtight, and there aren’t any signs of leaks.
Most often, his work aims to temporarily clear small bodies of water so site developers can work on the drainage systems. This means Souders must also revisit sites to remove the previously installed pipe plugs.
The main reason why Souders opts for Cherne pipe plugs is that he believes they are built better than any other on the market, making removal easier.
“They’re rugged and tough and can sustain rough handling,” he explains. “Because of how they are built, they last a long time in the water without degrading. The offset placement of the fittings makes removal easier than other plugs I’ve used.
“Typically,” he continues, “removing plugs is a nightmare on plugs with fittings in the center. Once air passes the fill point, it stops coming out, forcing me to use a specialized tool to remove the air.
“But the Cherne plugs are offset at the top. I simply open the fitting, and the air rushes out, allowing me to manually remove the pipe without needing any tools.”
Safety First
“Safety is the most important aspect of my job,” Souder stresses. “I’ve seen so many injuries that could have been prevented simply by implementing better safety measures.”
Souders’ focus on safety is very much in line with how Cherne operates. Cherne plugs offer best-in-class safety, durability, and premium performance. Safety is a top priority. Through rigorous quality control and state-of-the-art manufacturing technologies, Cherne products help ensure users will get the job done safely. Each pipe plug, no matter how big or small, undergoes multiple Quality Assurance processes, including a full inflation test. Again, Cherne tests every single plug that goes out, not to mention the quality, workmanship, and material quality of Cherne plugs.
Souders is passionate about educating young people about this lucrative and unorthodox career. He advises anyone looking to follow in his footsteps to learn to do the job safely through extensive training. Even then, safety precautions must always be in place in case of mishaps.